La fusione a cera persa consiste nel rivestire più strati di rivestimenti refrattari sulla superficie dello stampo in cera. Dopo che si è indurito ed essiccato, lo stampo in cera viene fuso mediante riscaldamento per ottenere un guscio con una cavità corrispondente alla forma dello stampo in cera. Dopo la cottura, viene colata in un metodo per ottenere fusioni, per questo viene chiamata anche fusione a cera persa. Con il continuo miglioramento della tecnologia di produzione, continuano ad apparire nuovi processi di stampaggio della cera e la varietà di materiali disponibili per lo stampaggio è in aumento. Ora il metodo di rimozione dello stampo non si limita più alla fusione e i materiali per stampaggio non si limitano più ai materiali in cera. Si possono utilizzare anche stampi in plastica. Poiché le fusioni ottenute con questo metodo hanno una maggiore precisione dimensionale e valori di rugosità superficiale inferiori, viene anche chiamata fusione di precisione.
La caratteristica fondamentale dicolata di investimentoè che per realizzare il guscio viene utilizzato uno stampo monouso fondibile. Poiché non è necessario imbutire lo stampo, il guscio è integrale senza superficie di separazione ed è realizzato con materiali refrattari con eccellenti prestazioni alle alte temperature. La microfusione può produrre getti di forma complessa, con uno spessore minimo della parete di 0,3 mm e un diametro minimo del foro di fusione di 0,5 mm. A volte nella produzione, alcune parti composte da più parti possono essere combinate in un tutto modificando la struttura e formate direttamente mediante fusione a cera persa. Ciò può far risparmiare ore di lavoro e consumo di materiale metallico e migliorare la struttura delparti di fusionepiù ragionevole.
Il peso dei getti prodotti mediante microfusione varia generalmente da decine di grammi a diversi chilogrammi, o addirittura decine di chilogrammi. Getti troppo pesanti non sono adatti alla microfusione a causa della limitazione delle prestazioni del materiale di stampaggio e della difficoltà nella realizzazione della conchiglia.
Getti prodotti tramite microfusionenon sono limitati dai tipi di leghe, soprattutto per le leghe difficili da tagliare o forgiare, che possono dimostrare la loro superiorità. Tuttavia, la produzione di microfusione presenta anche alcune carenze, principalmente dovute al gran numero di processi, lunghi cicli di produzione, processi tecnologici complessi e molti fattori che influenzano la qualità dei getti, che devono essere rigorosamente controllati per stabilizzare la produzione.
Rispetto ad altri metodi di fusione, la caratteristica notevole della fusione a cera persa è l'uso di stampi fusibili per realizzare la conchiglia. Ogni volta che viene prodotto un guscio viene consumato uno stampo di rivestimento. Il prerequisito necessario per ottenere getti di alta qualità con elevata precisione dimensionale e bassi valori di rugosità superficiale è uno stampo di rivestimento con elevata precisione dimensionale e bassi valori di rugosità superficiale. Pertanto, le prestazioni del materiale di stampaggio (denominato materiale dello stampo), la qualità dello stampaggio (il modello utilizzato per pressare il rivestimento) e il processo di stampaggio influenzeranno direttamente la qualità della fusione a cera persa.
Attualmente gli stampi per microfusione vengono generalmente utilizzati in un guscio realizzato con materiali refrattari multistrato. Dopo che il modulo è stato immerso e rivestito con rivestimento refrattario, cospargere il materiale refrattario granulare, quindi asciugarlo e indurirlo e ripetere questo processo molte volte fino a quando lo strato di materiale refrattario raggiunge lo spessore richiesto. In questo modo, sul modulo si forma un guscio multistrato, che solitamente viene parcheggiato per un periodo di tempo affinché si asciughi e indurisca completamente, e poi sformato per ottenere un guscio multistrato. Alcuni gusci multistrato devono essere riempiti di sabbia, altri no. Dopo la tostatura, possono essere versati direttamente, il che viene chiamato guscio ad alta resistenza.
La qualità della conchiglia è direttamente correlata alla qualità della fusione. In base alle condizioni di lavoro del guscio, i requisiti prestazionali del guscio includono principalmente:
1) Ha un'elevata resistenza alla temperatura normale, un'adeguata resistenza alle alte temperature e una bassa resistenza residua.
2) Ha una buona permeabilità all'aria (in particolare permeabilità all'aria alle alte temperature) e conduttività termica.
3) Il coefficiente di dilatazione lineare è piccolo, l'espansione termica è bassa e l'espansione è uniforme.
4) Eccellente resistenza al freddo e al caldo rapidi e stabilità termochimica.
Queste proprietà della conchiglia sono strettamente correlate ai materiali utilizzati nella fabbricazione della conchiglia e nel processo di fabbricazione della conchiglia. I materiali del guscio includono materiali refrattari, leganti, solventi, indurenti, tensioattivi, ecc. Tra questi, il materiale refrattario e il legante formano direttamente il guscio, che è il materiale principale del guscio. I materiali refrattari utilizzati nella fusione a cera persa sono principalmente sabbia silicea, corindone e refrattari di alluminosilicato (come argilla refrattaria e banadio di alluminio, ecc.). Inoltre, a volte vengono utilizzate sabbia di zircone e sabbia di magnesia.
Il materiale refrattario in polvere e il legante vengono preparati nel rivestimento refrattario, e il materiale refrattario granulare viene cosparso sul rivestimento refrattario quando viene realizzato il guscio. I leganti utilizzati nei rivestimenti refrattari comprendono principalmente l'idrolizzato di silicato di etile, il bicchiere d'acqua e il sol di silice. La vernice preparata con silicato di etile ha buone proprietà di rivestimento, elevata resistenza del guscio, piccola deformazione termica, elevata precisione dimensionale dei getti ottenuti e buona qualità superficiale. Viene utilizzato principalmente per produrre importanti getti di acciaio legato e altri getti con elevati requisiti di qualità superficiale. Il contenuto di SiO2 del silicato di etile prodotto in Cina è generalmente compreso tra il 30% e il 34% (frazione di massa), quindi è chiamato silicato di etile 32 (32 rappresenta la frazione di massa media di SiO2 nel silicato di etile). Il silicato di etile può svolgere un ruolo legante solo dopo l'idrolisi.
Il guscio di rivestimento preparato con vetro ad acqua è facile da deformare e rompersi. Rispetto al silicato di etile, i getti prodotti hanno una bassa precisione dimensionale e un'elevata rugosità superficiale. Il legante per vetro solubile è adatto per la produzione di piccole fusioni di acciaio ordinario egetti di leghe non ferrose. Il bicchiere d'acqua per la microfusione ha solitamente un modulo di 3,0~3,4 e una densità di 1,27~1,34 g/cm3.
Il legante sol di silice è una soluzione acquosa di acido silicico, noto anche come sol di silice. Il suo prezzo è 1/3~1/2 inferiore a quello del silicato di etile. La qualità dei pezzi fusi prodotti utilizzando il sol di silice come legante è superiore a quella del vetro solubile. L'agente legante è stato notevolmente migliorato. Il sol di silice ha una buona stabilità e può essere conservato a lungo. Non richiede indurenti speciali durante la realizzazione delle conchiglie. La resistenza alle alte temperature del guscio è migliore di quella dei gusci di silicato di etile, ma il sol di silice ha scarsa bagnabilità sul rivestimento e impiega più tempo per indurirsi. I principali processi di produzione del guscio comprendono lo sgrassaggio dei moduli, il rivestimento e la levigatura, l'essiccazione e l'indurimento, la sformatura e la tostatura.
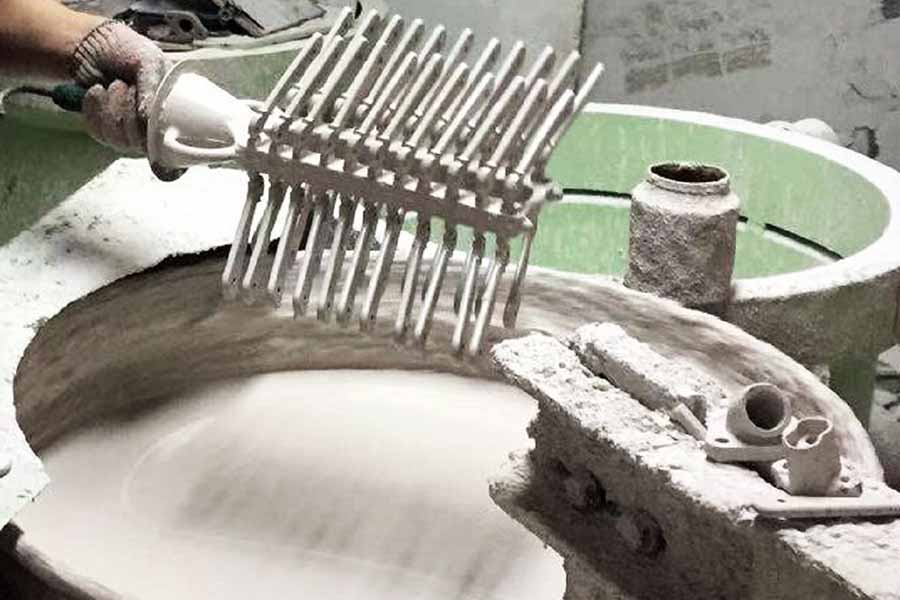
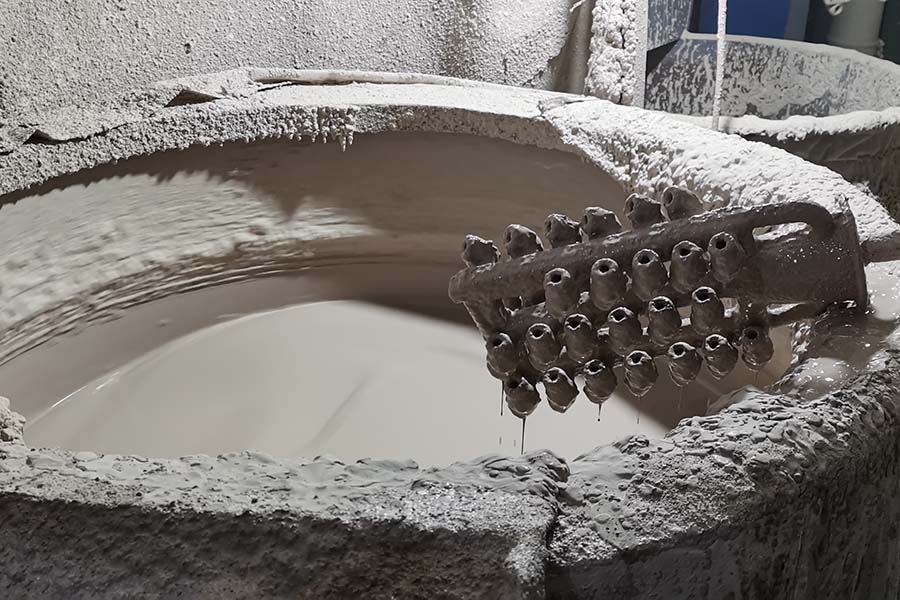
Orario di pubblicazione: 11 febbraio 2021