Azienda di fusione in sabbia di ghisa duttile dalla Cina con OEM personalizzato eServizi di lavorazione CNC.
La ghisa è una lega fusa ferro-carbonio con altri elementi, ottenuta rifondendo ghisa, rottami e altre aggiunte. Per differenziazione dall'acciaio e dall'acciaio colato, la ghisa è definita come una lega fusa con un contenuto di carbonio (min 2,03%) che garantisce la solidificazione della fase finale con trasformazione eutettica.
A seconda delle specifiche chimiche, le ghise possono essere non legate o legate. La gamma dei ferri legati è molto più ampia e contengono quantità maggiori di componenti comuni, come silicio e manganese, o aggiunte speciali, come nichel, cromo, alluminio, molibdeno, tungsteno, rame, vanadio, titanio, oltre a altri. In generale, la ghisa può essere divisa in ghisa grigia, ghisa duttile (ferro nodulare), ghisa bianca, ghisa a grafite compatta e ghisa malleabile.
Processo di fusione in conchigliaè anche chiamato processo di colata in sabbia di resina preverniciata, getti di stampaggio a conchiglia a caldo o processo di colata di anime. Il materiale principale per lo stampaggio è la sabbia di resina fenolica prerivestita, che è più costosa della sabbia verde e della sabbia di resina furanica. Inoltre, questa sabbia non può essere riciclata.
Le parti in fusione di ghisa in conchiglia hanno costi più elevati rispetto alla fusione in sabbia. Tuttavia, ilparti di fusione per stampaggio a conchigliapresentano molti vantaggi come una tolleranza dimensionale più stretta, una buona qualità della superficie e minori difetti di fusione.
▶ Materie prime per fusione in conchiglia:
• Acciaio al carbonio fuso: acciaio a basso tenore di carbonio, acciaio a medio carbonio e acciaio ad alto tenore di carbonio da AISI 1020 a AISI 1060.
• Leghe di acciaio fuso: 20CrMnTi, 20SiMn, 30SiMn, 30CrMo, 35CrMo, 35SiMn, 35CrMnSi, 40Mn, 40Cr, 42Cr, 42CrMo...ecc su richiesta.
• Acciaio inossidabile fuso: AISI 304, AISI 304L, AISI 316, AISI 316L e altri tipi di acciaio inossidabile.
• Leghe di alluminio fuso.
• Ottone e rame.
• Altri materiali e standard su richiesta
▶ Capacità di colata in conchiglia:
• Formato massimo: 1.000 mm × 800 mm × 500 mm
• Intervallo di peso: 0,5 kg - 100 kg
• Capacità annua: 2.000 tonnellate
• Tolleranze: A Richiesta.
▶ Ispezione dei componenti di precisione della fusione in conchiglia:
• Analisi quantitativa spettrografica e manuale
• Analisi metallografiche
• Controllo della durezza Brinell, Rockwell e Vickers
• Analisi delle proprietà meccaniche
• Test di impatto a temperatura normale e bassa
• Ispezione della pulizia
• Ispezione UT, MT e RT
▶ Procedure di fusione in conchiglia:
✔ Realizzazione di modelli in metallo. La sabbia di resina prerivestita deve essere riscaldata nei modelli, quindi i modelli in metallo sono gli strumenti necessari per realizzare getti in conchiglia.
✔ Realizzazione di stampi in sabbia preverniciati. Dopo aver installato i modelli in metallo sulla macchina per lo stampaggio, la sabbia di resina prerivestita verrà spruzzata nei modelli e, dopo il riscaldamento, il rivestimento in resina verrà fuso, quindi gli stampi in sabbia diventeranno gusci e nuclei di sabbia solidi.
✔ Fusione del metallo fuso. Utilizzando forni a induzione, i materiali verrebbero fusi in un liquido, quindi le composizioni chimiche del ferro liquido dovrebbero essere analizzate per corrispondere ai numeri e alle percentuali richiesti.
✔ Colata di metallo. Quando il ferro fuso soddisfa i requisiti, verrà versato negli stampi a conchiglia. In base alle diverse caratteristiche del progetto di fusione, gli stampi a conchiglia verranno sepolti nella sabbia verde o impilati a strati.
✔ Granigliatura, molatura e pulizia. Dopo il raffreddamento e la solidificazione delle fusioni, le colonne montanti, i cancelli o il ferro aggiuntivo devono essere tagliati e rimossi. Successivamente i getti di ferro verranno puliti mediante pallinatrici o granigliatrici. Dopo la rettifica della testa di colata e delle linee di divisione, arrivavano i pezzi finiti di fusione, in attesa di ulteriori processi, se necessari.
▶ Perché scegliere RMC per i componenti di fusione in conchiglia?
✔ Precisione e quindi elevato sfruttamento del materiale. Otterrai prodotti dalla forma netta o quasi netta dopo la fusione in shell moulding, a seconda delle esigenze degli utenti finali, il processo di lavorazione non sarà necessario o sarà richiesto un processo di lavorazione molto ridotto.
✔ Migliori prestazioni superficiali. Grazie ai materiali di nuova tecnologia per lo stampaggio, i getti da shell moulding hanno una superficie molto fine e di maggiore precisione.
✔ Una scelta equilibrata rispetto alla fusione in sabbia e al rivestimento. La fusione in conchiglia ha prestazioni e superficie migliori rispetto alla fusione in sabbia, pur avendo costi molto inferiori rispetto alla fusione a cera persa di precisione.
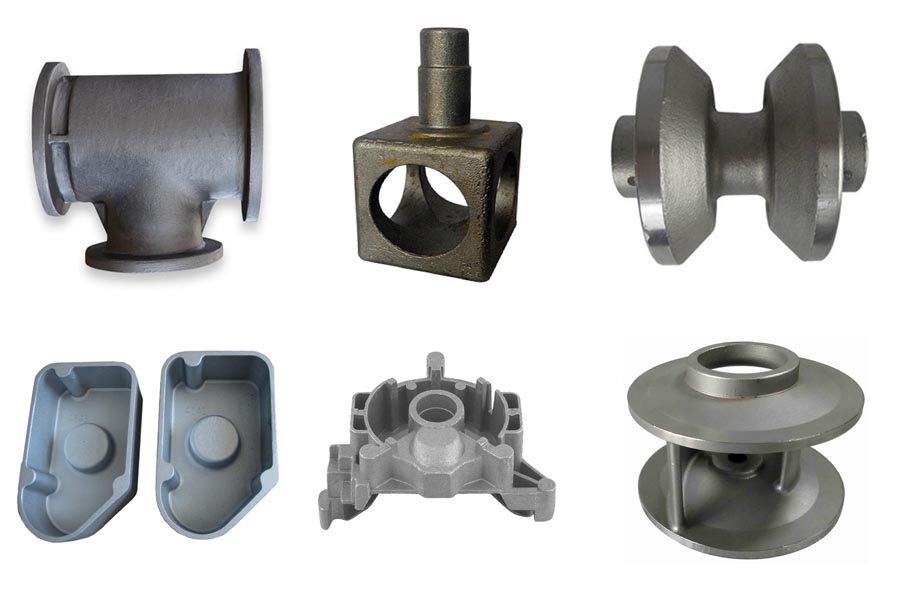